Power Electronics & Robotics – The energy supply of an AGV during operation (Part 3/5)
An automated material flow using AGVs, so-called “automated guided vehicles”, is associated with high acquisition costs. In order to achieve rapid amortisation of this investment, maximum utilisation of the vehicles must be ensured. On the one hand, this is realised through a storage system solution that is optimally designed for the general conditions and through intelligent software control. On the other hand, however, it must also be ensured that the AGVs have as little downtime as possible due to loading or servicing processes by operating them as efficiently as possible. In the following, various options for increasing efficiency are considered and their effects on the design of AGVs are analysed.
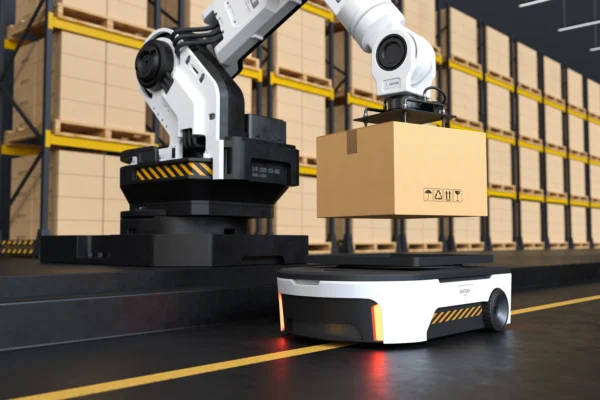
Discharging the energy storage system during operation
The discharge of an energy storage system during operation can vary depending on various framework conditions. For example, the payload, the acceleration and speed of various activities and the route profile all influence energy consumption. Intelligent control systems can optimise energy management by analysing energy consumption, navigating AGVs efficiently between their operating locations and distributing activities to different vehicles according to their charge status. However, this requires the precise and valid recording of various pieces of information and their transmission to the control system in real time.
Data acquisition and transmission
Application-specific decisions can or must be made on the basis of recorded temperature, current and voltage values. It is therefore important to interpret the data correctly. For example, thermal inertia plays an important role in temperature measurement, the voltage drop via the ohmic resistance of cables in voltage measurement or the high-frequency interference during the operation of electric motors in current measurement. In addition to hardware options, such as sense lines when recording voltages, the sampling rate and mathematical filters can also help to obtain valid values.
If the data relevant to sequence control is recorded by a central energy management unit in the form of a DC/DC converter, the bus load can be reduced during communication with the control unit, a standardised time stamp can be guaranteed and an immediate response can be made to critical operating conditions.
The supply of the drives
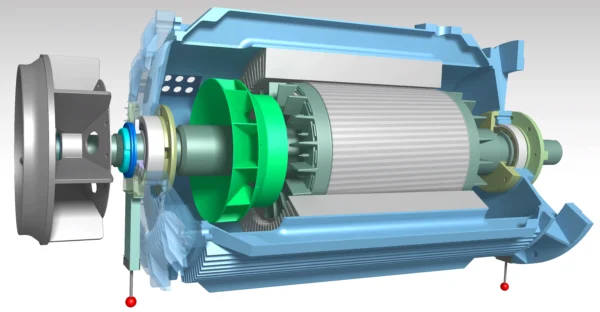
The supply voltage of electric motors influences their torque and speed. The efficiency of the drive also depends on the voltage applied, as the motor is usually designed to work optimally at a certain nominal voltage. For this reason, a regulated supply voltage is useful for high efficiency, as the clamping voltage of energy storage devices varies depending on the type and chemical composition of the state of charge and the current requirement.
To ensure a stable voltage supply even under fluctuating load conditions, an appropriately designed DC/DC converter, such as the DDL4848-48, is required. Depending on the length of the cables to the drive, cable compensation, i.e. increasing the voltage depending on the current flow, can also be useful here.
Increased efficiency through regenerative braking
As described at the beginning, the operating time of the AGV is decisive for the efficiency and amortisation period of the warehouse. It therefore makes sense not to burn energy via resistors during braking or lowering processes, but to feed it back into the energy storage system. The prerequisite for this is that the installed DC/DC converter is able to transfer energy bidirectionally, i.e. in both directions. During recuperation, i.e. regeneration, the vehicle’s electric motors act as generators and behave accordingly as a voltage source. A suitable DC/DC converter recognises this and then changes the direction of energy flow back into the energy storage system. Depending on the design and operation of the vehicles, this can increase efficiency and thus extend the runtime until the next charging stop by up to 40%.
Another positive aspect of energy recovery is that less heat is generated in the vehicle, as the braking energy is converted into electrical energy rather than heat.
Conclusion
Overall, recuperation using bidirectional DC/DC converters in AGVs offers a win-win situation by improving energy efficiency, lowering operating costs, reducing environmental impact and optimising vehicle performance.